Sensing Fiber Optic Cables for Maritime Use: Types, Specs, and Offshore Applications
Discover high-performance sensing fiber optic cables engineered for maritime environments. Learn about FA, FB, GYXG, and GYXGS types, their technical specifications, and key roles in ports, vessels, and offshore monitoring systems.
BLOGS
6/6/202514 min read
Introduction
In the demanding world of maritime operations, where salt spray, extreme temperatures, and constant mechanical stress are everyday realities, traditional sensing solutions often fall short. This is where sensing fiber optic cables emerge as game-changing technology, offering unprecedented reliability and performance in some of the harshest environments on Earth.
Sensing fiber optic cables represent a sophisticated evolution of standard fiber optic technology, specifically engineered to withstand the unique challenges of maritime environments while providing real-time monitoring capabilities. Unlike conventional fiber optic cables designed primarily for communication, these specialized cables integrate sensing capabilities directly into their structure, allowing them to detect changes in temperature, strain, pressure, and other critical parameters along their entire length.
The maritime industry's growing reliance on these advanced sensing systems stems from their ability to provide continuous, real-time monitoring of critical infrastructure across ports, vessels, and offshore platforms. From monitoring the structural integrity of massive container cranes to detecting temperature variations in subsea cables, sensing fiber optic cables have become indispensable tools for ensuring safety, optimizing operations, and preventing costly failures in maritime environments.
What makes these cables particularly valuable in maritime applications is their inherent resistance to electromagnetic interference, their ability to operate over vast distances without signal degradation, and their capacity to provide distributed sensing along their entire length. This means that a single cable can monitor conditions across kilometers of infrastructure, providing detailed spatial and temporal data that would be impossible to achieve with traditional point sensors.
Categories of Sensing Fiber Optic Cables
Understanding the different categories of sensing fiber optic cables is crucial for selecting the right solution for specific maritime applications. Each type has been engineered with particular strengths and characteristics that make it suitable for different environmental conditions and operational requirements.
FA Type: Compact High-Compression Solutions
The FA type sensing fiber optic cable represents the pinnacle of compact design without compromising performance. Its structure consists of optical fibers housed within a stainless steel tube, which is then protected by an outer aluminum tube. This dual-tube configuration creates a robust yet lightweight solution that excels in applications where space is at a premium.
The most notable feature of FA type cables is their exceptional compression resistance combined with their compact size. The stainless steel inner tube provides immediate protection for the optical fibers, while the aluminum outer tube adds an additional layer of protection against environmental factors. This design philosophy makes FA type cables particularly suitable for installations where cables must navigate tight spaces or be integrated into existing structures without significant modifications.
In maritime environments, FA type cables shine in applications such as monitoring equipment mounted on vessel decks, where space constraints are common and the cable must withstand the constant compression forces from foot traffic, equipment placement, and deck operations. The compact nature of these cables also makes them ideal for retrofitting existing maritime infrastructure with sensing capabilities.
FB Type: Hybrid Power and Signal Transmission
The FB type cable takes the robust design of the FA type and adds integrated metal conductors, creating a hybrid solution that can simultaneously transmit optical signals and electrical power. This dual-functionality represents a significant advancement in cable technology, as it eliminates the need for separate power and signal cables in many applications.
The structural design of FB type cables maintains the stainless steel tube housing for the optical fibers while incorporating carefully designed metal conductors that can carry electrical current without interfering with the optical signals. This integration requires precise engineering to ensure that the electrical and optical components work harmoniously without introducing noise or signal degradation.
For maritime applications, FB type cables offer tremendous value in situations where both sensing data and electrical power need to be transmitted to remote locations. This is particularly common in offshore platforms, where sensors and monitoring equipment are often located far from primary power sources. Instead of running separate cables for power and data, a single FB type cable can handle both functions, reducing installation complexity, maintenance requirements, and overall system costs.
GYXG Type: High Tensile Strength for Dynamic Applications
The GYXG type cable is specifically engineered for applications involving dynamic cable movement and high mechanical stress. Its structure features a central stainless steel tube surrounded by stranded steel wires, creating a cable with exceptional tensile strength and flexibility. This design allows the cable to withstand the constant movement and mechanical stress common in maritime environments.
The stranded steel wire reinforcement gives GYXG type cables their characteristic high tensile strength, making them capable of supporting their own weight over long spans while maintaining signal integrity. The central stainless steel tube continues to provide protection for the optical fibers, ensuring that the sensing capabilities remain intact even under significant mechanical stress.
These cables are particularly valuable in dynamic maritime applications such as monitoring systems on floating platforms, where the cable must accommodate the constant movement of the platform with ocean swells. They are also excellent choices for crane applications, where the cable must flex and move repeatedly as the crane operates, while continuing to provide accurate sensing data throughout its operational life.
GYXGS Type: Extreme Environment Performance
The GYXGS type represents the most robust category of sensing fiber optic cables, designed to operate in the most extreme conditions encountered in maritime environments. Its structure incorporates a small-diameter stainless steel tube with additional armor and insulation layers, creating a cable capable of withstanding temperatures from -196°C to +300°C while maintaining mechanical integrity.
The additional armor and insulation layers in GYXGS type cables provide protection against not only temperature extremes but also chemical exposure, mechanical damage, and long-term environmental degradation. This makes them the preferred choice for applications where cables must operate reliably for extended periods in harsh conditions without the possibility of easy replacement or maintenance.
In maritime applications, GYXGS type cables are essential for monitoring systems in engine rooms, where high temperatures are common, as well as in cryogenic storage areas on LNG carriers, where extremely low temperatures would destroy lesser cables. Their extreme temperature resistance also makes them suitable for monitoring heated pipelines and equipment in offshore oil and gas operations.
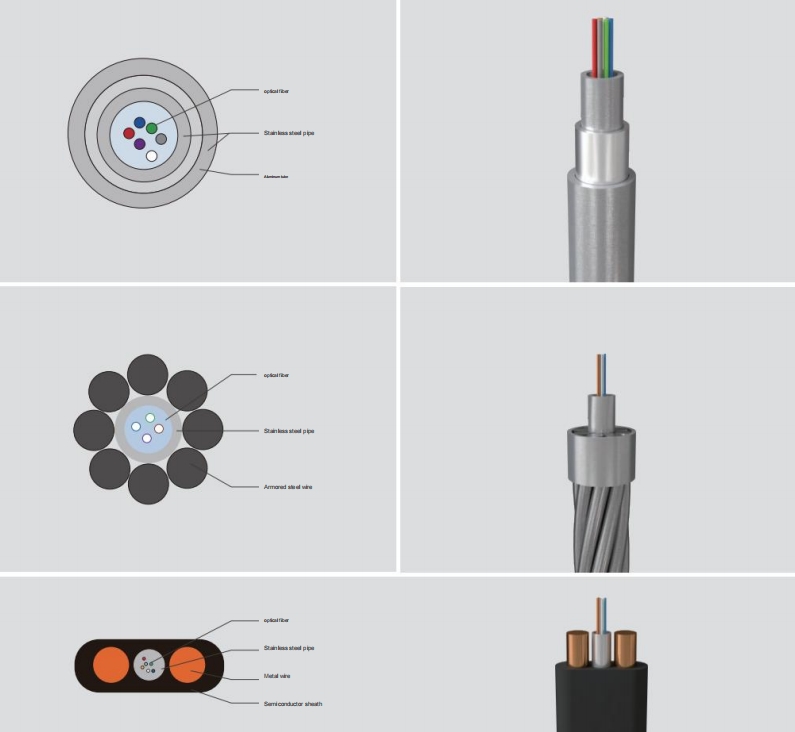
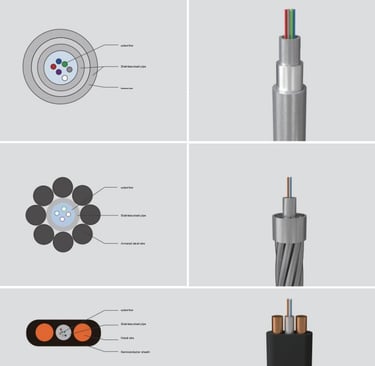
Electrical and Mechanical Performance Parameters
Understanding the technical specifications of sensing fiber optic cables is essential for proper selection and application in maritime environments. These parameters define the operational limits and capabilities of each cable type, providing the foundation for engineering decisions and system design.
Fiber Core Count and Configuration
The number of optical fiber cores within a sensing cable directly impacts its monitoring capabilities and application flexibility. Most maritime sensing applications utilize cables with one to eight fiber cores, with each core capable of independent sensing or communication functions. Single-core configurations are often sufficient for simple temperature or strain monitoring along a linear path, while multi-core configurations enable more complex sensing arrays or provide redundancy for critical applications.
The configuration of multiple cores within a cable also affects the types of sensing that can be performed. Some advanced applications use multiple cores to create sensing arrays that can detect not only the magnitude of changes but also their direction and spatial distribution. This capability is particularly valuable in structural health monitoring applications, where understanding the complete stress state of a structure is crucial for safety assessment.
Compression Resistance Specifications
Compression resistance is a critical parameter for maritime applications, where cables may be subjected to significant crushing forces from equipment, cargo, or operational activities. FA and FB type cables demonstrate exceptional performance in this area, with compression resistance ratings up to 20,000 N per 100mm of cable length. This specification means that these cables can withstand substantial crushing forces without damage to the internal optical fibers.
The ability to withstand high compression forces is particularly important in port environments, where cables may be installed in areas with heavy vehicle traffic or where cargo handling equipment operates. The high compression resistance ensures that the sensing capabilities remain intact even when cables are accidentally stepped on or subjected to the weight of heavy equipment.
Operating Temperature Ranges
Temperature performance varies significantly among cable types, with each designed for specific temperature ranges based on their intended applications. Standard FA and FB types typically operate effectively in temperature ranges from -40°C to +85°C, which covers most maritime environmental conditions. However, the GYXGS type extends this range dramatically, operating from -196°C to +300°C, enabling applications in extreme temperature environments.
The extended temperature range of GYXGS type cables opens up possibilities for monitoring applications that would be impossible with standard cables. In maritime environments, this capability enables monitoring of cryogenic storage systems, high-temperature engine components, and heated pipelines that operate well outside the temperature range of conventional sensing systems.
Bending Radius Requirements
The minimum bending radius specifications are crucial for cable installation and long-term reliability. These specifications are typically given for both dynamic and static applications, recognizing that cables used in moving applications require different flexibility characteristics than those in fixed installations.
For dynamic applications, minimum bending radii typically range from 20 to 25 times the cable diameter, ensuring that the cable can flex repeatedly without damage to the internal optical fibers. Static applications allow for tighter bend radii, typically 10 to 15 times the cable diameter, since the cable will not be subjected to repeated flexing once installed.
Understanding these bending radius requirements is essential for proper cable routing and installation design. Violations of minimum bending radius specifications can lead to immediate damage to optical fibers or gradual degradation that reduces the cable's operational life and sensing accuracy.
Tensile Strength Characteristics
Tensile strength specifications define the maximum pulling forces that cables can withstand during installation and operation. These specifications are typically given for both short-term and long-term loading conditions, recognizing that cables may need to withstand brief high loads during installation while operating under lower sustained loads during normal operation.
Short-term tensile strength ratings can reach up to 4,000 N for robust cable types, allowing for significant pulling forces during installation through cable trays, conduits, or other routing infrastructure. Long-term tensile strength ratings, typically around 2,000 N, define the maximum sustained load that cables can support during normal operation without degradation.
These tensile strength characteristics are particularly important for vertical installations, where cables must support their own weight over long distances, and for applications where cables are subjected to dynamic loading from equipment movement or environmental forces such as wave action on offshore platforms.
Typical Applications in Maritime Environments
The versatility and robustness of sensing fiber optic cables make them suitable for a wide range of maritime applications, each taking advantage of different aspects of the technology's capabilities. Understanding these applications helps illustrate the practical value of these specialized cables in real-world maritime operations.
Port Crane Structure Monitoring
Port cranes represent some of the most critical and expensive infrastructure in maritime operations, making their continuous monitoring essential for safe and efficient operations. Sensing fiber optic cables installed throughout crane structures can provide real-time monitoring of structural stress, temperature variations, and mechanical deformation that might indicate developing problems before they become critical failures.
The installation of sensing cables on port cranes typically involves routing FA or GYXG type cables along critical structural members, where they can detect changes in strain that might indicate structural fatigue or overloading. The cables can also monitor temperature variations in electrical components and mechanical systems, providing early warning of potential equipment failures that could result in costly downtime or safety hazards.
The distributed sensing capability of these cables means that a single cable installation can monitor the entire crane structure, providing detailed spatial information about stress distribution and identifying specific locations where problems may be developing. This comprehensive monitoring capability enables predictive maintenance strategies that can prevent failures and optimize crane utilization.
Subsea Cable Sensing Applications
Subsea cables represent critical infrastructure for maritime operations, carrying power, communications, and control signals to offshore platforms and underwater equipment. The harsh subsea environment, with its combination of high pressure, corrosive seawater, and mechanical stresses from currents and marine life, makes monitoring of these cables essential for reliable operation.
Sensing fiber optic cables integrated into subsea cable systems can provide continuous monitoring of temperature and strain along the entire cable length. Temperature monitoring is particularly important for power cables, where overheating can indicate insulation degradation or overloading conditions that could lead to cable failure. Strain monitoring can detect cable movement, damage from fishing activities, or anchor strikes that might compromise cable integrity.
The ability to precisely locate problems along subsea cables is one of the most valuable aspects of distributed fiber optic sensing. Traditional monitoring methods can only detect that a problem exists somewhere along a cable, but distributed sensing can pinpoint the exact location of the problem, dramatically reducing the time and cost required for repairs.
Structural Health Monitoring on Ships and Offshore Platforms
Ships and offshore platforms operate in environments where structural integrity is critical for safety and operational effectiveness. The constant stresses from wave action, cargo loading, and operational activities can cause fatigue and damage that may not be visible during routine inspections. Sensing fiber optic cables provide a means for continuous monitoring of structural health, enabling early detection of problems before they become critical.
On ships, sensing cables can be installed along critical structural members such as the hull, deck beams, and cargo hold supports. These installations can monitor stress levels during different loading conditions, helping to optimize cargo loading patterns and detect potential structural problems before they affect safety or operational capability.
Offshore platforms present particularly challenging monitoring requirements due to their exposure to harsh environmental conditions and the critical nature of their operations. Sensing cables installed throughout platform structures can monitor for fatigue damage, foundation settlement, and environmental loading that might affect platform stability or operational safety.
Hybrid Power and Signal Transmission Systems
Many maritime applications require both sensing data and electrical power to be transmitted to remote locations, making FB type cables with their integrated power and signal capabilities particularly valuable. These hybrid cables eliminate the complexity and cost of running separate power and signal cables while providing the robustness needed for maritime environments.
Offshore wind farms represent an excellent example of hybrid cable applications, where individual turbines require both power transmission and continuous monitoring of various parameters such as vibration, temperature, and structural stress. FB type cables can handle both the power transmission requirements and the sensing data collection, simplifying the overall system architecture and reducing installation and maintenance costs.
Similarly, offshore oil and gas platforms often have monitoring equipment located at remote locations that require both power and data connectivity. Hybrid sensing cables can provide both functions while withstanding the harsh environmental conditions common in these applications.
Practical Considerations for Maritime Use: Frequently Asked Questions
Understanding the practical aspects of sensing fiber optic cable applications helps maritime professionals make informed decisions about system design and implementation. These frequently asked questions address common concerns and considerations encountered in real-world maritime applications.
What Makes Sensing Cables Different from Traditional Fiber Optics?
The fundamental difference between sensing fiber optic cables and traditional communication fiber optic cables lies in their construction and intended application. While traditional fiber optic cables are designed primarily to transmit data signals with minimal loss, sensing cables are engineered to detect and measure changes in their environment while maintaining signal transmission capabilities.
The stainless steel armoring and ruggedized design of sensing cables provide mechanical protection and corrosion resistance that far exceeds that of traditional fiber optic cables. This enhanced protection is essential in maritime environments, where cables are exposed to salt spray, mechanical stress, and environmental conditions that would quickly degrade traditional cables.
Additionally, sensing cables are designed to work with specialized interrogation equipment that can detect minute changes in the optical properties of the fiber caused by temperature variations, mechanical strain, or other environmental factors. This capability transforms the cable from a passive transmission medium into an active sensing system that can provide detailed information about conditions along its entire length.
Can These Cables Operate in Cryogenic or High-Temperature Zones?
The temperature operating range of sensing fiber optic cables varies significantly depending on the cable type and construction. Standard FA and FB type cables typically operate effectively in temperature ranges from -40°C to +85°C, which covers most maritime environmental conditions encountered in normal operations.
However, GYXGS type cables are specifically designed for extreme temperature applications and can operate reliably from -196°C to +300°C. This extended temperature range makes them suitable for monitoring cryogenic storage systems on LNG carriers, where temperatures can reach extremely low levels, as well as high-temperature applications such as engine room monitoring or heated pipeline systems.
The ability to operate in extreme temperatures is achieved through specialized materials selection and construction techniques that maintain the integrity of both the optical fibers and the protective structures surrounding them. The additional insulation and armor layers in GYXGS type cables provide thermal protection while maintaining the flexibility and sensing capabilities of the cable.
How Are These Cables Installed on Dynamic Equipment Like Cranes?
Installing sensing cables on dynamic equipment such as cranes requires careful consideration of the mechanical stresses and movement patterns that the cables will experience during operation. FA and GYXG type cables are particularly well-suited for these applications due to their high compression resistance and flexible bending characteristics.
The installation process typically involves routing cables along crane structures in ways that minimize stress concentrations while providing adequate protection from mechanical damage. This often requires the use of specialized cable management systems, including flexible cable carriers, protective conduits, and strain relief systems that can accommodate the repetitive motion of crane operations.
The key to successful installation on dynamic equipment is understanding the movement patterns and stress distributions that occur during normal operation. This requires close collaboration between cable manufacturers, crane engineers, and installation specialists to develop routing schemes that provide reliable sensing performance while maintaining the mechanical integrity of both the cable and the crane structure.
Are These Cables Suitable for Combined Power and Sensing Functions?
FB type sensing cables are specifically designed to provide both power transmission and sensing capabilities in a single cable assembly. These hybrid cables include integrated metal conductors that can carry electrical current while maintaining the optical fibers needed for sensing applications.
The power carrying capacity of FB type cables is typically sufficient for powering remote sensing equipment, monitoring systems, and small electronic devices. However, the power levels are generally limited compared to dedicated power cables, making them most suitable for applications requiring modest power levels rather than high-power transmission.
The advantage of hybrid cables is the simplification of system architecture and installation complexity. Instead of requiring separate power and signal cables, a single FB type cable can handle both functions, reducing installation costs, maintenance requirements, and the overall complexity of the monitoring system.
What About Salt Spray Corrosion Concerns?
Salt spray corrosion is one of the most significant challenges in maritime environments, and sensing fiber optic cables are specifically designed to address this concern. The stainless steel tubing used in all types of sensing cables provides excellent resistance to salt spray corrosion, maintaining protective integrity even after extended exposure to marine environments.
The sealed design of sensing cables prevents salt water intrusion into the cable structure, protecting the optical fibers and other internal components from corrosive effects. Additional protective measures, such as specialized jacket materials and sealing compounds, further enhance the corrosion resistance of these cables.
Long-term testing in marine environments has demonstrated that properly selected and installed sensing cables can provide reliable operation for many years in salt spray conditions. Regular inspection and maintenance procedures can further extend cable life and ensure continued reliable operation in challenging maritime environments.
Conclusion
The evolution of sensing fiber optic cables represents a significant advancement in maritime monitoring and safety technology. Through understanding the distinct characteristics and capabilities of different cable types, maritime professionals can select and implement sensing solutions that provide reliable, long-term monitoring capabilities in even the most challenging environmental conditions.
The FA type cables offer compact, high-compression solutions ideal for space-constrained applications, while FB type cables provide the added benefit of hybrid power and signal transmission capabilities. GYXG type cables excel in dynamic applications requiring high tensile strength and flexibility, and GYXGS type cables push the boundaries of environmental tolerance to enable monitoring in extreme temperature conditions.
The key to successful implementation of sensing fiber optic cables in maritime applications lies in careful selection based on the specific mechanical, electrical, and environmental requirements of each application. Understanding the performance parameters, installation requirements, and operational characteristics of each cable type enables maritime professionals to design monitoring systems that provide valuable operational data while maintaining the reliability and safety standards required in maritime operations.
As maritime operations continue to evolve toward greater automation and condition-based maintenance strategies, sensing fiber optic cables will play an increasingly important role in enabling the real-time monitoring and data collection capabilities needed to support these advanced operational concepts. The investment in proper sensing cable selection and installation today provides the foundation for safer, more efficient maritime operations in the future.