H07VVH6-F PVC Trailing Cables: Essential Power Solutions for Maritime Lifting and Hoisting Equipment
Comprehensive guide to H07VVH6-F PVC trailing cables for maritime cranes and hoisting equipment. Learn about technical specifications, applications in Singapore ports, installation best practices, and performance in harsh marine environments.
BLOGS
7/7/202510 min read
Introduction: The Critical Role of Electrical Infrastructure in Maritime Operations
In the bustling maritime industry, where massive container ships dock at ports like Singapore's PSA International terminals and heavy-duty cranes orchestrate the precise choreography of cargo handling, electrical reliability forms the backbone of operational success. Every day, thousands of twenty-foot equivalent units (TEUs) move through these facilities, powered by sophisticated electrical systems that demand robust, dependable cabling solutions.
The selection of appropriate trailing cables for maritime lifting and hoisting equipment represents far more than a simple procurement decision. It constitutes a critical safety and efficiency consideration that directly impacts operational continuity, worker safety, and equipment longevity. In environments where salt spray, temperature fluctuations, mechanical stress, and moisture exposure create a perfect storm of challenging conditions, the wrong cable choice can lead to catastrophic failures, costly downtime, and potentially dangerous situations.
This is where the H07VVH6-F PVC flat cable emerges as a specialized solution designed specifically to meet the demanding requirements of maritime crane systems, port gantry operations, and shipboard hoisting equipment. Understanding its capabilities, limitations, and proper application becomes essential for maritime engineers, port operators, and vessel maintenance professionals who must ensure reliable power delivery in some of the most challenging industrial environments on Earth.
Technical Foundation: Dissecting the H07VVH6-F PVC Cable Design
Construction Architecture: Building Resilience from the Inside Out
The H07VVH6-F cable represents a carefully engineered solution where each component serves a specific purpose in delivering reliable electrical performance under maritime conditions. At its core lies a flexible class 5 stranded copper conductor that complies with IEC 60228 standards, a specification that might seem like mere technical jargon but actually defines the very foundation of the cable's mechanical flexibility and electrical performance.
To understand why this matters, consider the alternative: solid copper conductors, while excellent for fixed installations, would quickly fail under the constant flexing demands of a container crane's cable reel system. The class 5 stranding, consisting of numerous fine copper wires twisted together, allows the conductor to bend repeatedly without work-hardening and eventual fracture. This becomes particularly crucial in applications like Singapore's automated container terminals, where cranes operate continuously, subjecting cables to millions of flex cycles over their service life.
The PVC insulation layer surrounding each conductor incorporates HD-308 core identification, utilizing either color-coding or numerical marking systems to ensure proper circuit identification during installation and maintenance. This feature proves invaluable in complex maritime electrical systems where a single crane might incorporate dozens of circuits for motors, controls, lighting, and safety systems. The ability to quickly and accurately identify specific conductors can mean the difference between a minor maintenance issue and extended downtime that costs thousands of dollars per hour.
Encasing the entire cable assembly, the flame-retardant PVC outer sheath meeting IEC 60332-1 standards provides the critical barrier against environmental hazards and fire propagation. This flame-retardant property becomes particularly significant in maritime applications where electrical faults in confined spaces, such as ship engine rooms or crane operator cabins, could quickly escalate into life-threatening situations.
Electrical Performance Parameters: Understanding the Numbers Behind Safe Operation
The voltage rating of 450/750 V AC positions the H07VVH6-F cable squarely in the low-voltage category, making it ideal for auxiliary power systems rather than main propulsion or high-power applications. This voltage level aligns perfectly with the requirements of most crane control systems, work lighting, and ancillary equipment found in port operations. The test voltage of 2500 VAC provides a substantial safety margin, ensuring that the cable can withstand voltage spikes and transients common in industrial electrical systems.
The insulation resistance specification of at least 20 megohms per kilometer represents the cable's ability to prevent current leakage between conductors and to ground. In maritime environments where moisture can infiltrate even well-sealed systems, this high insulation resistance provides crucial protection against ground faults that could trip protective devices or, worse, create dangerous touch potentials on metal equipment frames.
Mechanical Properties: Flexibility Meets Durability
The minimum bending radius specification of ten times the cable diameter reflects a careful balance between flexibility and mechanical integrity. For a typical 20mm diameter cable, this translates to a minimum bend radius of 200mm, which accommodates the tight routing requirements of crane cable reels while preventing conductor damage. This specification becomes particularly relevant when designing cable management systems for applications like the massive ship-to-shore cranes at Singapore's Tanjong Pagar Terminal, where cables must navigate complex routing paths while maintaining electrical integrity.
The operating temperature ranges tell an important story about the cable's versatility. The moving application range of -25°C to +70°C covers the vast majority of maritime operating conditions, from cold winter operations in northern ports to the intense heat of tropical engine rooms. The static temperature range extending down to -40°C ensures that cables remain serviceable even during extreme cold weather storage or in refrigerated container handling areas.
Maritime Applications: Where Theory Meets Harsh Reality
Shipyard and Port Operations: The Proving Ground for Cable Performance
In Singapore's Jurong Shipyard, one of the world's largest ship repair facilities, H07VVH6-F cables find extensive application in mobile cranes used for lifting heavy engine components, propellers, and structural assemblies. These operations demand cables that can withstand not only the mechanical stresses of heavy lifting but also exposure to cutting oils, hydraulic fluids, and the corrosive effects of salt air. The PVC sheath construction provides excellent resistance to many industrial chemicals while maintaining flexibility even after prolonged exposure to oil vapors common in shipyard environments.
Container terminal operations present another demanding application scenario. The massive rail-mounted gantry cranes at PSA's Pasir Panjang Terminal move hundreds of containers daily, with trailing cables providing power to trolley motors, hoist mechanisms, and spreader positioning systems. The continuous duty cycle in these applications makes cable reliability paramount, as a single cable failure can shut down an entire crane bay, backing up vessel operations and potentially causing significant economic losses.
Vessel Maintenance and Dry Dock Operations
Floating dry docks and ship repair facilities represent some of the most challenging environments for electrical cables. The combination of high humidity, temperature variations, mechanical vibration, and exposure to various chemicals creates conditions that can quickly degrade inferior cable products. H07VVH6-F cables have proven particularly effective in these applications, providing reliable power to portable welding equipment, work lighting systems, and material handling gear used in vessel maintenance operations.
The flat cable configuration offers distinct advantages in these applications, allowing for more efficient cable management in tight spaces while providing multiple circuits in a single cable assembly. This becomes particularly valuable in temporary installations where minimizing cable runs and connection points reduces both installation time and potential failure modes.
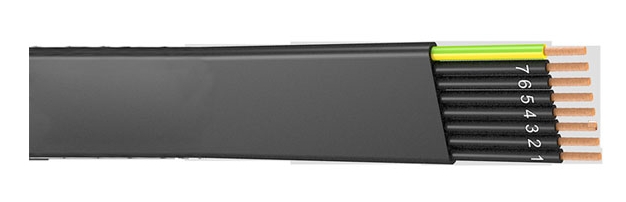
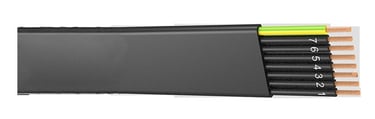
Addressing Common Maritime Challenges: Practical Solutions for Real-World Problems
Moisture and Water Exposure: Managing the Inevitable
Maritime environments present an ongoing battle against moisture intrusion, and understanding the H07VVH6-F cable's capabilities and limitations in wet conditions requires careful consideration. The PVC insulation and sheath materials provide good moisture resistance for typical maritime applications, effectively protecting against spray, condensation, and brief water exposure. However, it's crucial to understand that these cables are not designed for continuous submersion or use in areas subject to pressure washing or heavy rain without additional protection.
In practical terms, this means that while these cables perform excellently on covered crane runways or in semi-protected shipboard locations, installations in fully exposed deck areas may require additional protective measures such as cable guards, drainage provisions, or periodic replacement schedules to account for accelerated aging due to moisture exposure.
Fire Safety in Confined Spaces: Beyond Basic Compliance
The flame-retardant properties of the H07VVH6-F outer sheath represent more than simple regulatory compliance; they constitute a critical safety feature in maritime applications where fire can spread rapidly through ventilation systems and confined spaces. The IEC 60332-1 standard ensures that the cable will not propagate flame when subjected to a standardized flame source, but proper installation practices must complement this inherent safety feature.
This includes maintaining adequate spacing between cables and heat sources, ensuring proper circuit protection to prevent overload conditions, and implementing regular thermal imaging inspections to identify potential hot spots before they become fire hazards. In Singapore's maritime sector, where strict safety regulations govern both port operations and vessel maintenance activities, these considerations become part of comprehensive safety management systems.
Dynamic Loading and Mechanical Stress: Engineering for Movement
The trailing cable applications in maritime cranes subject cables to complex mechanical stresses that go far beyond simple bending. The combination of tension from the cable's own weight, dynamic loading from crane acceleration and deceleration, and torsional stress from cable reel rotation creates a challenging mechanical environment. The H07VVH6-F cable's class 5 stranded construction and specified bending radius help manage these stresses, but proper installation techniques remain crucial for achieving maximum service life.
Cable support systems must be designed to minimize stress concentrations while allowing for normal operational movement. This often involves careful calculation of cable sag distances, selection of appropriate cable clamps and guides, and implementation of strain relief measures at connection points. In large crane installations, computer modeling of cable behavior under various loading conditions has become standard practice to optimize both performance and service life.
Temperature Extremes and Thermal Management
While Singapore's tropical climate might suggest that cold weather performance is irrelevant, maritime operations often involve vessels and equipment that have operated in various global climates. Cables installed during cold weather conditions or stored in air-conditioned facilities must maintain flexibility and electrical properties across the entire specified temperature range.
The thermal characteristics of PVC insulation also require consideration in high-temperature applications. While the H07VVH6-F cable can operate continuously at temperatures up to 70°C, sustained operation at these extreme temperatures will accelerate aging and may require more frequent inspection and replacement schedules. Proper ventilation and heat dissipation become critical factors in enclosed installations such as crane operator cabins or equipment compartments.
Voltage Limitations and System Compatibility
The 450/750 V rating of H07VVH6-F cables makes them unsuitable for medium-voltage ship service applications, which typically operate at 3.3 kV or higher. This limitation must be clearly understood during system design to prevent inappropriate application. However, for the vast majority of crane and hoisting equipment applications, this voltage level provides an optimal balance between safety and performance.
The cable's electrical characteristics also make it well-suited for variable frequency drive (VFD) applications common in modern crane control systems. The low capacitance and good insulation properties help minimize electromagnetic interference while providing reliable power transmission for sophisticated electronic control systems.
Service Life and Maintenance Considerations
Predicting cable service life in maritime applications requires understanding the cumulative effects of environmental exposure, mechanical stress, and operational duty cycles. While H07VVH6-F cables can provide many years of reliable service under proper conditions, harsh maritime environments may accelerate aging through several mechanisms.
Salt spray exposure can cause gradual degradation of the outer sheath, particularly at termination points where moisture can penetrate protective covers. Ultraviolet radiation from intense tropical sunlight can cause surface cracking and hardening of PVC materials. Mechanical abrasion from contact with cable guides and supports gradually wears away protective sheaths, potentially exposing internal components to environmental attack.
Regular inspection programs become essential for maintaining electrical safety and preventing unexpected failures. These inspections should include visual examination of the outer sheath for cracks, cuts, or signs of chemical attack, electrical testing to verify insulation resistance and continuity, and thermal imaging to identify overheating conditions that might indicate impending failure.
Installation Excellence: Best Practices for Maritime Environments
Cable Routing and Support Systems
Proper cable routing in maritime applications requires careful attention to both mechanical and environmental factors. Cable trays and guides must be designed to accommodate thermal expansion and contraction while preventing mechanical damage from contact with sharp edges or other equipment. In corrosive maritime environments, the selection of appropriate materials for support hardware becomes critical to prevent galvanic corrosion and ensure long-term reliability.
The flat configuration of H07VVH6-F cables offers advantages in space-constrained installations but requires careful attention to mounting orientation to prevent deformation under the cable's own weight. Vertical runs should incorporate intermediate supports to prevent excessive stress on termination points, while horizontal runs must account for thermal expansion that can create substantial forces in constrained routing systems.
Environmental Protection Strategies
While H07VVH6-F cables provide good inherent environmental resistance, additional protective measures may be warranted in particularly harsh applications. Cable conduits or protective covers can shield cables from direct spray, mechanical impact, and ultraviolet exposure. However, these protective systems must be designed to allow for cable movement and thermal dissipation while preventing moisture accumulation that could accelerate degradation.
Drainage provisions become particularly important in covered installations where water might accumulate around cable routing systems. Proper slope design and drainage points help ensure that moisture does not pool around cables, reducing the risk of insulation degradation and corrosion of metallic components.
Connection and Termination Practices
Cable terminations represent critical points where environmental protection must be maintained while providing reliable electrical connections. Marine-grade connectors and junction boxes designed for the specific environmental conditions become essential components of the overall system. These connections must provide not only electrical continuity but also environmental sealing to prevent moisture intrusion that could compromise system reliability.
Proper strain relief at termination points helps prevent mechanical damage to conductors and maintains the integrity of environmental seals. In applications subject to continuous movement, such as crane cables, these strain relief systems must accommodate the full range of motion while preventing fatigue failure of both the cable and termination hardware.
Conclusion: Integrating Knowledge into Maritime Operations
The H07VVH6-F PVC trailing cable represents a specialized solution developed to meet the unique challenges of maritime lifting and hoisting applications. Its combination of mechanical flexibility, environmental resistance, and electrical performance makes it well-suited for the demanding conditions found in port operations, shipyards, and vessel maintenance facilities. The cable's compliance with international IEC standards provides assurance of quality and performance while facilitating global procurement and standardization efforts.
Understanding the technical capabilities and limitations of these cables enables maritime professionals to make informed decisions about their application while implementing appropriate installation and maintenance practices. The key to successful cable performance lies not only in proper product selection but also in comprehensive system design that considers environmental conditions, mechanical stresses, and operational requirements.
Regular maintenance and inspection programs remain essential for ensuring continued electrical safety and operational reliability. As maritime operations continue to evolve with increasing automation and more demanding operational schedules, the electrical infrastructure that supports these activities must provide unwavering reliability. The H07VVH6-F cable, when properly applied and maintained, contributes to this reliability while helping ensure the safety of personnel and equipment in challenging maritime environments.
For maritime operators in Singapore and around the world, understanding these technical considerations and implementing best practices in cable selection, installation, and maintenance represents an investment in operational reliability and safety that pays dividends through reduced downtime, lower maintenance costs, and enhanced safety performance. As the maritime industry continues to evolve, the electrical systems that power this evolution must be designed and maintained to the highest standards of excellence.
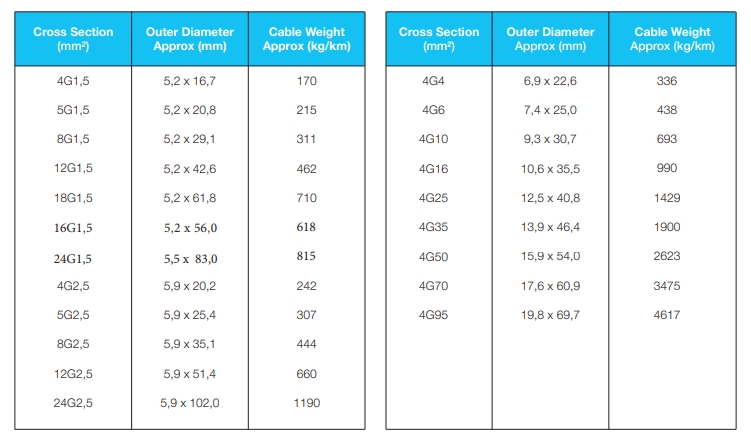
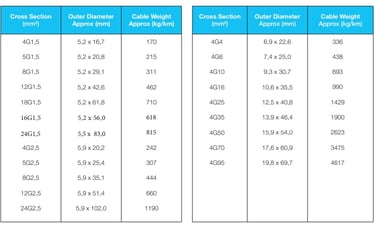