FRHF-IXO(i)SA 150/250V Cable for Marine and Offshore: Fire-Resistant Instrumentation with Superior EMI Protection
Explore the FRHF-IXO(i)SA 150/250V cable, a fire-resistant, halogen-free marine instrumentation cable engineered for offshore and shipboard use. Featuring individual pair shielding and high EMI resistance, it ensures reliable signal transmission in harsh environments.
BLOGS
7/1/202510 min read
Introduction: The Hidden Backbone of Marine Communication
When we observe a massive container vessel navigating through Singapore's bustling port or witness an offshore oil platform operating seamlessly in harsh ocean conditions, we rarely consider the intricate network of cables that makes such precision possible. Yet beneath the steel decks and behind control panels lies a sophisticated web of instrumentation and control cables that serve as the nervous system of modern maritime operations.
Signal integrity in marine environments presents unique challenges that land-based installations rarely encounter. The combination of electromagnetic interference from powerful engines, saltwater corrosion, extreme temperature fluctuations, and the constant vibration of ocean waves creates an environment where standard cables simply cannot maintain the reliability required for critical operations. When a navigation system receives corrupted data or a fire suppression system fails to respond due to signal degradation, the consequences extend far beyond equipment failure—they threaten lives and valuable assets.
This is precisely why specialized marine instrumentation cables like the FRHF-IXO(i)SA have become indispensable in modern maritime engineering. These cables represent years of engineering refinement, designed specifically to maintain signal fidelity in the most demanding marine environments while meeting stringent international safety standards.
Understanding the FRHF-IXO(i)SA 150/250V Cable
The FRHF-IXO(i)SA cable stands as a sophisticated solution engineered for the demanding world of marine instrumentation and control systems. This fire-resistant, individually screened cable represents a convergence of advanced materials science and practical marine engineering requirements.
At its core, this cable serves as a reliable conduit for transmitting critical data and control signals in environments where failure is not an option. Whether installed in the engine room of a cargo vessel navigating through Singapore's port facilities or integrated into the control systems of an offshore wind farm, the cable must maintain signal integrity across multiple pairs simultaneously while withstanding the harsh realities of marine service.
The cable finds its primary applications in marine vessels, offshore platforms, and coastal telecommunication infrastructure where individual pair screening becomes essential for preventing cross-talk between signal channels. In complex marine systems, where dozens of sensors, actuators, and control devices must communicate reliably, the ability to isolate each signal pair from electromagnetic interference becomes crucial for maintaining operational safety and efficiency.
The designation "individually screened" represents a fundamental design philosophy that recognizes the reality of modern marine operations. Unlike simpler cables that rely on overall screening alone, this approach acknowledges that in densely packed cable runs common to ships and offshore platforms, individual signal pairs require their own protective barriers against electromagnetic interference.
Design Features that Define Performance Excellence
The conductor system forms the foundation of the cable's reliability, utilizing tinned copper stranded conductors manufactured to Class 2 specifications according to IEC 60228. This choice of tinned copper over bare copper represents a critical design decision for marine applications. The tin coating provides superior resistance to corrosion in the salt-laden atmosphere of marine environments, while the stranded construction offers the flexibility necessary for installation in the confined spaces typical of ship construction.
The fire resistance characteristics emerge from a carefully engineered insulation system combining mica tape and cross-linked polyethylene (XLPE). Mica tape serves as a mineral-based barrier that maintains its insulating properties even when exposed to extreme temperatures during fire conditions. This material continues to protect the conductor's electrical integrity long after organic materials would have degraded, allowing critical safety systems to continue operating during emergency situations.
The cable's architecture reveals its sophisticated approach to electromagnetic compatibility. Each individual pair receives its own screening consisting of aluminum-mylar tape combined with a tinned copper drain wire. This arrangement creates what engineers call a "Faraday cage" around each signal pair, effectively isolating it from external electromagnetic fields while providing a low-impedance path for any induced currents to return to ground safely.
Over this individual screening system, a copper wire braiding provides an additional layer of electromagnetic shielding. This braided construction offers superior flexibility compared to solid metal screens while maintaining excellent shielding effectiveness across a broad frequency spectrum. The braiding also provides mechanical protection for the internal components during installation and service.
The outer sheath utilizes SHF1 halogen-free compound available in both orange and blue color options. This material choice reflects growing environmental consciousness in marine applications, as halogen-free materials produce fewer toxic gases during combustion compared to traditional PVC compounds. The color coding serves practical purposes in complex installations, allowing technicians to quickly identify different cable circuits or systems.
Inner filler materials and tape bindings contribute to the cable's mechanical stability by maintaining the precise geometry of internal components during bending and flexing. These seemingly minor components play crucial roles in maintaining the cable's electrical characteristics throughout its service life by preventing conductor migration and maintaining consistent spacing between signal pairs.
Technical Performance Parameters
The voltage rating of 150/250V with a nominal operating voltage of 300V provides adequate safety margins for typical marine instrumentation applications while allowing for voltage variations common in shipboard electrical systems. This rating reflects careful consideration of the voltage levels encountered in modern marine control and monitoring systems.
Thermal performance specifications reveal the cable's ability to operate across the extreme temperature ranges encountered in marine service. The operating temperature rating of +90°C accommodates installation in engine rooms and other high-temperature marine environments, while the short circuit temperature rating of +250°C ensures that the cable maintains its integrity during electrical fault conditions long enough for protective systems to respond.
The cold resistance specification down to -40°C for fixed installations addresses the reality that marine vessels and offshore platforms operate in polar regions where ambient temperatures can reach extreme lows. This specification ensures that the cable materials remain flexible and maintain their electrical properties even under these harsh conditions.
Bending radius specifications directly impact installation practices aboard ships and offshore platforms where space constraints often require cables to navigate tight corners and confined spaces. The specified minimum bending radius ensures that the internal screening systems maintain their effectiveness while preventing damage to the conductor insulation during installation.
Fire Safety and Environmental Compliance Standards
The flame retardance characteristics meeting IEC 60332-1-2 and IEC 60332-3-22 Category A standards address two distinct fire scenarios common in marine applications. The single cable flame test (IEC 60332-1-2) ensures that an individual cable will not propagate flame when exposed to a standard ignition source, while the bundled cable test (IEC 60332-3-22 Cat A) addresses the more challenging scenario where multiple cables installed together might contribute to fire spread.
Fire resistance performance according to IEC 60331-1, IEC 60331-2, and IEC 60331-21 standards represents a higher level of fire performance. These tests evaluate the cable's ability to continue operating during direct flame exposure, ensuring that critical safety systems such as fire detection, emergency lighting, and communication systems remain functional during fire emergencies. This capability can prove life-saving in marine environments where evacuation options may be limited.
The low smoke emission characteristic tested per IEC 61034-2 addresses visibility concerns during fire emergencies. In the confined spaces typical of ships and offshore platforms, smoke generation can quickly reduce visibility to dangerous levels, hampering evacuation efforts and firefighting activities. Low smoke cables help maintain visibility corridors during emergencies.
Halogen-free properties verified according to IEC 60754-1 standards eliminate the production of toxic and corrosive gases during combustion. Traditional cables containing halogens release hydrogen chloride and other toxic gases when burned, creating additional hazards for personnel and causing long-term corrosion damage to nearby equipment. The halogen-free formulation addresses both immediate safety concerns and long-term equipment protection.
Low corrosivity performance per IEC 60754-2 quantifies the cable's environmental impact during combustion by measuring the acidity of gases produced. This specification becomes particularly important in marine environments where sensitive electronic equipment must continue operating in adjacent spaces during and after fire incidents.
Electrical Parameters and Signal Quality Assurance
Conductor resistance specifications provide the foundation for calculating power losses and voltage drops in extended cable runs common to large vessels and offshore installations. The resistance values for both 0.75mm² and 1.5mm² conductor sizes allow engineers to select the appropriate conductor size based on circuit length and current requirements while maintaining signal integrity.
Insulation resistance specifications ensure that each conductor pair maintains proper isolation from adjacent pairs and from ground, preventing signal degradation through leakage currents. High insulation resistance becomes particularly critical in marine environments where moisture intrusion can gradually degrade insulation performance over time.
Loop inductance values directly affect the cable's performance in high-frequency applications common to modern digital communication systems. Lower inductance values allow for higher data transmission rates while maintaining signal quality, making these specifications crucial for telecommunications and advanced control system applications.
Nominal capacitance values for different conductor sizes influence the cable's characteristic impedance and signal propagation characteristics. These parameters become increasingly important as marine systems incorporate higher frequency digital communications and precision analog measurement systems where signal reflection and distortion must be minimized.
Understanding these electrical parameters helps system designers optimize cable selection for specific applications. For instance, longer cable runs may require larger conductor sizes to maintain acceptable voltage drops, while high-frequency applications may demand specific impedance characteristics to prevent signal reflections.
International Standards and Classification Society Approvals
Compliance with IEC 60228 ensures that conductor construction meets internationally recognized standards for flexibility, current-carrying capacity, and mechanical strength. This standard provides the foundation for reliable electrical connections and long-term conductor integrity across varying temperature and mechanical stress conditions.
The IEC 60092 series of standards specifically addresses electrical installations in ships, covering everything from cable construction to installation practices. Compliance with these standards ensures that the cable meets the unique requirements of marine electrical systems, including enhanced moisture resistance, vibration tolerance, and electromagnetic compatibility.
Recognition by major classification societies including DNV (Det Norske Veritas), ABS (American Bureau of Shipping), BV (Bureau Veritas), CCS (China Classification Society), and LR (Lloyd's Register) provides third-party verification of the cable's suitability for marine applications. These organizations maintain rigorous testing and certification programs that evaluate not only the cable's technical performance but also the manufacturer's quality control processes.
Type approval from classification societies streamlines the approval process for shipbuilders and marine operators by providing pre-approved cable specifications that meet regulatory requirements. This approval process reduces project risks and ensures compliance with international maritime safety regulations while providing assurance of long-term reliability in service.
Real-World Applications in Marine Environments
Engine rooms present some of the most challenging electromagnetic environments found aboard ships, with powerful electric motors, generators, and switching equipment creating intense electromagnetic fields across a broad frequency spectrum. In these environments, the individually screened pairs of the FRHF-IXO(i)SA cable provide essential protection for instrumentation signals monitoring engine parameters, fuel systems, and safety equipment.
Control rooms, while typically cleaner environments, require exceptional signal integrity for navigation systems, communication equipment, and vessel management systems. The precision required for modern GPS navigation, radar systems, and automated vessel control systems demands cables capable of maintaining signal fidelity over extended periods while resisting the gradual degradation that can occur in marine atmospheres.
Singapore's port operations provide an excellent example of these cables in action. The port's advanced container handling systems rely on precise positioning data and real-time communication between automated cranes, vehicle guidance systems, and central control computers. The electromagnetic environment created by multiple electric motors, radio communications, and electronic systems requires instrumentation cables capable of maintaining signal integrity in this electrically noisy environment.
Long-term fixed installations in offshore platforms must withstand not only the immediate challenges of salt spray and temperature extremes but also the gradual effects of UV exposure, thermal cycling, and mechanical stress from platform movement. The cable's robust construction and materials selection specifically address these long-term reliability requirements.
Frequently Asked Questions About Cable Selection
When considering these cables for intrinsically safe zones, it's important to understand that while the cable itself may be suitable for such installations, the complete system including terminations, barriers, and associated equipment must receive appropriate certification for intrinsically safe applications. The cable's construction provides excellent signal integrity, but intrinsic safety requires consideration of the entire electrical circuit.
The benefit of individual pair screening versus overall screening becomes apparent in applications where multiple signal types share the same cable run. Overall screening protects all pairs from external interference but provides no protection against crosstalk between pairs within the cable. Individual pair screening addresses both external interference and inter-pair crosstalk, making it essential for applications requiring high signal integrity across multiple channels.
Compared to non-armoured instrumentation cables, the FRHF-IXO(i)SA cable provides superior electromagnetic protection through its copper wire braiding while maintaining the flexibility required for marine installations. Armoured cables offer enhanced mechanical protection but often sacrifice flexibility and electromagnetic performance, making them less suitable for applications where both mechanical protection and signal integrity are required.
The choice between different screening approaches often depends on the specific electromagnetic environment and signal requirements of the application. Applications with high-frequency digital signals typically benefit from individual pair screening, while simple analog measurements may perform adequately with overall screening alone.
Conclusion: Engineering Reliability into Marine Operations
The FRHF-IXO(i)SA cable represents more than simply another component in a marine electrical system—it embodies the engineering philosophy that reliability cannot be compromised when lives and valuable assets depend on proper system operation. Through its sophisticated screening architecture, fire-resistant materials, and rigorous compliance with international standards, this cable provides the signal integrity foundation that modern marine operations demand.
The cable's individual pair screening technology addresses the fundamental challenge of maintaining clean signals in the electromagnetically hostile environment of ships and offshore platforms. By providing each signal pair with its own protective barrier, the cable ensures that critical instrumentation and control systems receive the clean, accurate data necessary for safe and efficient operation.
Environmental compliance through halogen-free materials and low smoke emission characteristics reflects the marine industry's growing awareness of environmental responsibility while providing practical benefits for personnel safety during emergency situations. These features demonstrate how modern cable technology can simultaneously address performance, safety, and environmental concerns.
The extensive approval by international classification societies provides assurance that the cable meets the rigorous standards demanded by marine applications while simplifying the approval process for system integrators and vessel operators. This recognition reflects years of proven performance in demanding marine environments around the world.
As marine systems continue to incorporate more sophisticated digital technologies and higher levels of automation, the importance of reliable signal transmission becomes even more critical. The FRHF-IXO(i)SA cable's robust design and proven performance characteristics position it to meet the evolving needs of marine instrumentation and control systems while maintaining the reliability that maritime operations demand.
In the complex world of marine engineering, where failure is not an option and safety cannot be compromised, choosing the right instrumentation cable becomes a critical decision that impacts both immediate operational success and long-term reliability. The FRHF-IXO(i)SA cable provides the signal integrity, fire safety, and environmental compliance necessary to meet these demanding requirements while delivering the performance that modern marine operations require.
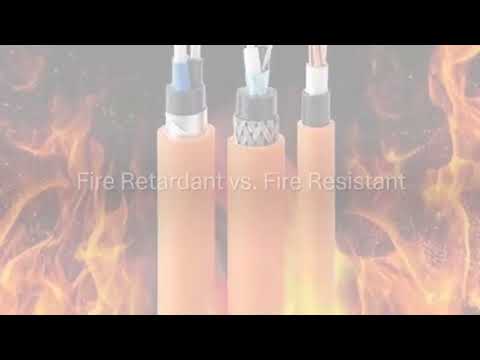